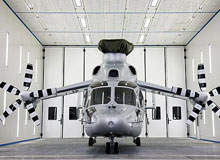
The Eurocopter X3 is a high-speed, long-range hybrid technology demonstrator helicopter being designed and manufactured by Eurocopter SAS. It will be one of the fastest fixed wing helicopters in the world with a projected speed of over 220kt (407km per hour).
The helicopter’s maiden flight took place on 6 September 2010 in southern France at the Istres Center of DGA Flight Testing. The X3’s initial flight test began in September 2010 with the goal of achieving a 180kt (333km per hour) speed by December 2010. The helicopter achieved 180kt speed on 29 November 2010 at an altitude of 3,810m during its second flight test.
On attaining the 180kt speed, the X3 underwent a gearbox upgrade and safety inspection to accomplish its target speed of 220kt (407km per hour).
During the third flight test conducted on 12 May 2011, the helicopter accomplished a true speed of 232kt (430km per hour) for several minutes at full power. Flight tests continued through 2011 to examine the helicopter’s full flight envelope.
Eurocopter X3 fixed-wing helicopter design
The Eurocopter X3 was designed to execute both military and civil missions. The helicopter can perform civil roles including long-distance search and rescue (SAR) missions, coastguard duties, border patrol missions, passenger transport and inter-city shuttle services.
It can carry out military operations including special forces operations, troop transport, combat search and rescue (CSAR) and medical evacuation.
The helicopter is fitted with a five-bladed main rotor system on the upper section of fuselage. It is equipped with two vertical propellers on short-span fixed wings on either side of the fuselage.
The incorporation of main rotor system and vertical propellers allows the helicopter to attain speeds equivalent to turboprop-powered aircraft, while providing full hover flight capabilities.
The helicopter has been designed to integrate forward-facing propeller engines with two short aircraft wings and main rotor blades. Auxiliary propellers render propulsive force in forward flight and anti-torque control in hover. The demonstrator overcomes the main rotor system damage, which occurs when the rotor tips achieve supersonic speeds.
Development
In an effort to reduce the development effort and cost, Eurocopter engineers have built components from the existing models. The fuselage is similar to that of AS365 N3 Dauphin. The company has adopted main rotor system from EC155. The main gear box was developed based on the EC175 with two additional drives for propellers.
Eurocopter launched the helicopter in January 2008 after working secretly for a long time. Rolls-Royce unveiled the selection of its RTM 322 turboshaft engine for the Eurocopter X3 programme during the Helicopter Association International’s Heli-Expo trade show in Anaheim, California in February 2009.
Eurocopter is also planning to build a 20-seat X3 variant, which will weigh around 30,000lbs (13,607kg) by 2018. This variant will be deployed for offshore applications.
Features of the Eurocopter X3
The X3 features a Dauphin-series fuselage, conventional empennage and modern flight control system. The helicopter is also fitted with vertical take-off and landing (VTOL) system which executes vertical take-off and landing by using the higher cruise speeds of rotor tips and vertical propellers.
Cockpit and cabin
The X3 features a partial glass cockpit to accommodate two crew members including pilot and co-pilot. It also has a large cabin that can be configured to house either cargo or passengers.
Eurocopter X3 Rolls-Royce Turbomeca RTM322 turboshaft engines
The Eurocopter X3 is powered by two Rolls-Royce Turbomeca RTM322 turboshaft engines. Each engine can produce 1,735kW of output power. The RTM322 engine is built jointly by Rolls-Royce and Turbomeca.
The length and diameter of the engine are 1.17m and 0.64m, respectively. Its basic weight is 539lb (234kg).
The engine is fitted with a three-stage axial and close coupled centrifugal compressor impelled by a two-stage gas generator turbine. It is also incorporated with full authority digital engine control (FADEC) system to provide automated flight controls with the intervention of a pilot.
An epicyclic speed reduction gearbox integrated in the engine decreases propeller noise by optimising output speed.
Health and usage monitoring system is installed in the powerplant to render wide range of engine diagnostic capabilities.