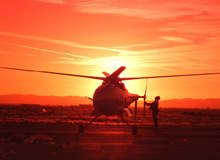
The A160 Hummingbird long-endurance helicopter UAV is capable of carrying out persistent intelligence, surveillance and reconnaissance, target acquisition, communications relay and precision resupply missions. The air vehicle, with optimum-speed rotor, operates autonomously and flies at 260km/h at a maximum altitude of 9,150m, with a hover capability up to 4,570m for up to 20 hours.
Boeing Integrated Defence Systems, advanced systems division is building three A160 Hummingbird UAVs for the US Defense Advanced Research Projects Agency (DARPA) and eight for the US Special Operations Command (SOCOM).
The production A160T Hummingbird, with a Pratt & Whitney PW207D turboshaft engine for increased range and longer endurance, completed its first flight in June 2007 at Boeing’s airfield in Victorville, California. Previous flight testing was carried out using a six-cylinder gasoline engine.
A160 Hummingbird unmanned helicopter development
In May 2008, the A160T successfully completed all 14 phase I flight test demonstrations, including: flight at a maximum speed of 263km/h (142kt), an eight-hour flight carrying a 450kg (1,000lb) payload, an 18.7-hour endurance flight with a 136kg (300lb) payload and a high-altitude hover-out-of-ground effect (HOGE) demonstration at 4,572m (15,000ft) and 6,000m (20,000ft).
The capabilities of such high-hover altitudes and payloads enable the A160 to detect slow moving targets and provide high-end detection of potential threats.
The vehicle’s technology and reliability will be consolidated to use the aircraft with a number of sensor programmes under an eight-month bridge phase by DARPA which ran from March 2008. The programme is continuing with an additional 60 hours of flight envelope expansion and 250 hours of ground testing.
In December 2008, Boeing announced that the A160T Hummingbird had achieved the use of a two-speed transmission to change gears in flight on 25 November 2008, and that the craft had transcended the 100-flight-hour mark on 20 November 2008. These tests were conducted under the $5m bridge contract between Boeing and DARPA.
In October 2009, Boeing and CSC were awarded a $5bn contract by the Special Operations Forces Support Activity (SOFSA) to provide comprehensive logistics support services to US Special Operations Command. The ten-year contract will include providing maintenance and repairs, supply chain and asset management, and information technology to enhance processes and systems within SOFSA.
The A160T helicopter will take part in the US Marine Corps warfighting laboratory’s immediate cargo unmanned aerial system demonstration programme.
A160 UAV programme
Frontier Systems based in Irvine, California, was contracted in 1998 by DARPA to develop and build a high-endurance stealthy surveillance helicopter with a target specification of endurance 30 to 48 hours, a service ceiling of 16,750m and range on internal fuel of up to 5,500km which represented a performance of typically double that of then-current rotor aircraft.
Frontier Systems was awarded additional project funding under the US Army’s future combat systems programme. The first prototype A160 Hummingbird, with a three-bladed main rotor, took its maiden flight in December 2001, prior to the conversion of the other prototypes to four-bladed helicopters.
Boeing acquired Frontier Systems in 2004 and the development of the A160 was transferred to the company’s Phantom Works and then to the integrated defence systems business division of Boeing. The first flight of the Boeing A160 Hummingbird took place in September 2004.
In August 2005, Boeing Frontier Systems was contracted by the US Navy Air Warfare Center to carry out a three-year programme advanced concept technology demonstration (ACTD) to assess the application of the military applications of a vertical take-off and landing UAV with various interchangeable and variable payloads.
The A160 programme has completed ten years as an experimental rotary-wing UAV with SOCOM. The aircraft is currently being tested for demonstration as a strike weapon after completing the 18.7-hour endurance milestone. SOCOM also stated that the aircraft would be fitted with air-to-ground missiles for these tests.
Under the programme, seven Hummingbird prototypes were delivered by Boeing to SOCOM. In addition, SOCOM has plans to secure another 20 A160T Hummingbirds to be deployed as strike and surveillance aircraft on field from 2012 to 2017.
Further new sensor systems have been designed to fly with the A160s. To provide long-term surveillance, the foliage penetration reconnaissance, surveillance, tracking and engagement radar (FORESTER) system was designed for A-160T Hummingbird.
About 20 flight tests of the A160T Hummingbird unmanned helicopter with FORESTER were completed in October 2009. The tests began on 31 August 2009 and were conducted at Fort Stewart, Georgia, US.
Hummingbird air vehicle
The air vehicle is a rotor-wing aircraft with a four-bladed main rotor and a two-bladed tail rotor mounted on the tail port side. The main rotor was three-bladed in the original prototype vehicle, which crashed twice during test flights. The helicopter design was then re-engineered and modified to a four-bladed main-rotor design.
The rotor and blade designs are innovative: the main rotor is hingeless and the semi-rigid blades are of carbon-fibre construction, with larger diameter, lower disc loading and lower tip speeds compared to conventional rotors with the same lift capability.
The revolution rate (rpm) of the rotor can be reduced by more than half its maximum, which contributes to an increase in the air vehicle’s fuel efficiency in low-speed and low-weight flight. In contrast, conventional rotors are designed to operate at maximum revolution rates. The low rotor speed contributes to the exceptionally low acoustic signature of the helicopter.
The blades’ stiffness and thickness, and the chord ratio are tapered from blade root to the blade tip, resulting in a flexible tip and less-flexible root and providing higher performance in terms of an increased lift-to-drag ratio. The lighter weight and stiffness of the blades contribute to reducing vibration problems.
The fuselage is of carbon-fibre construction and is of a smooth aerodynamic design which also gives low radar and visual signatures. The helicopter is fitted with a stabilising rectangular underfin and retractable wheeled landing gear.
The air vehicle is capable of conventional and autonomous landing and take-off.
Payloads
The height of the landing gear provides 0.84m ground clearance under the fuselage for the turret. A large mission payload bay is installed in the nose of the vehicle and a sensor turret can be installed under the nose section of the fuselage.
Payload options include: day and night electro-optical and infrared imaging systems, radar with synthetic aperture radar (SAR) / moving target indicator (MTI) modes and with foliage penetration capability and a laser target designator. The air vehicle can also be fitted with electronic countermeasures payloads, satellite communications and a datalink transmitter / receiver.
Control and navigation
The helicopter flies autonomously with manual override. The UAV’s flight control system was designed by Frontier Systems. Navigation includes global positioning and GPS-based waypoint navigation. Frontier Systems developed and validated the basic versions of the hardware and software for Hummingbird’s autonomous flight control early in the development programme using a Robinson R22 helicopter.
Engine
The A160T Hummingbird is powered by a single Pratt & Whitney Canada PW207D turboshaft engine. The engine can produce a continuous 426.7kW (572shp).
The engine also features a full authority digital engine control (FADEC) facility to reduce the workload of the pilot, including self-starting and fuel consumption. It also comprises a single stage centrifugal compressor, reverse flow combustor, single-stage high-pressure and shrouded power turbines.
The length and height of the engine are 0.91m and 0.56m respectively. The width and diameter are 0.5m and 0.55m respectively.