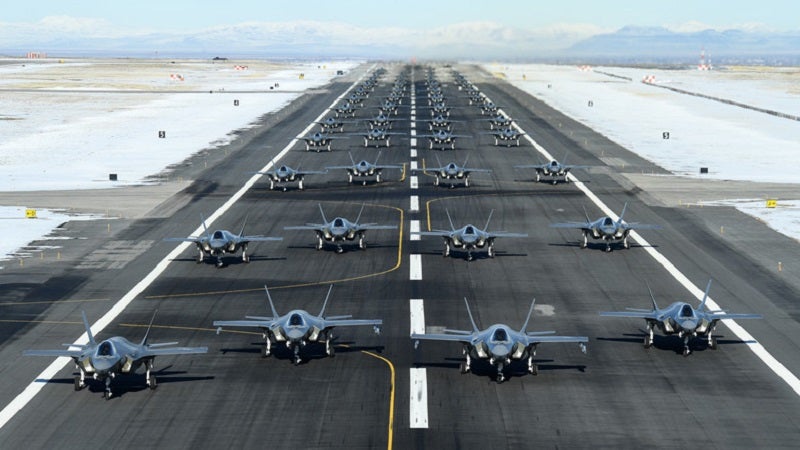
The F-35 programme has found new sources for over 1,000 components for the fighter that were being made in Turkey, however, there are 15 ‘key parts’ that are not being manufactured at the needed production rate to build the aircraft.
The GAO report said: “According to programme officials, some suppliers for the F-35 struggled to meet increased production demands in 2019 and, as a result, the program witnessed increased rates of late deliveries or parts shortages.”
The US ejected Turkey from the F-35 Joint Strike Fighter programme in 2019.
The issues with replacing the Turkish supply chain are compounded by existing supplier problems that have seen late deliveries of F-35 components increase from 2,000 to 10,000 between August 2017 and July 2019.
Between July 2018 and July 2019, the GAO found that the monthly parts shortage had increased from 875 to 8,000 components. Roughly 60% of parts shortages are down to just 20 suppliers, the report adds.
On top of the supply chain issues, the GAO noted that F-35 Block 4 cost has increased by $1.5bn to $12.1bn. However, this cost estimate may not be accurate, with the GAO adding: “The cost estimate did not fully adhere to leading practices, such as including all life cycle costs.”
Another risk for the programme is that only 3,000 of the programme’s over 10,000 suppliers meet ‘predefined design standards for ensuring product quality’. On top of this, of the aircraft fielded so far, over 500 do not meet reliability and maintenance goals.
The GAO report reads: “Although the contractor is changing manufacturing processes to address problems and improve efficiency, more remains to be done. Unless the programme office evaluates the risks of not meeting these leading practices, the military services and international partners are at risk of not receiving the quality aircraft they purchased”
The report also highlights that in 2019, 91% of engines for the fighter were delivered late, even though in the same period Pratt & Whitney did increase engine production by 51%. The GAO added: “In 2019, the airframe contractor was able to work around the late engine deliveries to deliver the entire aircraft on time.”
Overall, however, Lockheed Martin has improved on-time deliveries as the production of the aircraft has ramped up. In 2019, only 17 of 134 F-35s were delivered late, in comparison to 38 of 91 aircraft being delivered late in 2018.
Since 2016, the proportion of ammunition delivered on time has increased year on year.
Image: GAO
Open and closed deficiencies
The F-35 has long been plagued by several category 1 and 2 deficiencies hampering the aircraft’s effectiveness. In 2019, over 300 F-35 deficiencies were resolved, however, in the same period another 331 were discovered during operational testing. As of December 2019, 870 open deficiencies were left to be resolved.
As it stands there are 9 open category 1 deficiencies, and 861 category 2 faults.
Category 1 deficiencies are seen by the Department of Defence (Dod) as critical problems that could affect the safety and security of the fighter. Category 2 deficiencies are seen as faults that could affect or constrain successful mission accomplishment.
Of the 9 open Cat 1 deficiencies, the DoD has ‘operational workarounds’ for all of them, the report added: “The program office plans to continue to address the open deficiencies, but officials report that some will not be fully resolved for several years. Further, some deficiencies may not be resolved ever and some may be resolved well after the program has completed testing, and after it expects to have made a full-rate production decision.”
Despite the aircraft’s issues, the unit cost of the F-35 continues to fall. In October the DoD finalised a contract for lofts 12 through 14 for a total of 351 F-35As. This contract brings the unit cost per aircraft in loft 14 down to $73m.
As production lots have progressed the price per unit of the F-35 has seen a dramatic fall from over $200m per unit in lot 1.
Image: GAO.